Our Process
What to Expect During a Commercial Roofing Project
Commercial roofing projects follow a structured process—starting with condition assessment and ending in code-compliant installation. Understanding each stage helps property owners prepare for costs, minimize disruption, and extend roof lifespan, especially in Central Pennsylvania’s variable climate.
Our Process for Safe & Effective Roofing
Equity Roofing uses a step-by-step approach to deliver roofing systems that meet performance standards, safety codes, and building-specific needs.
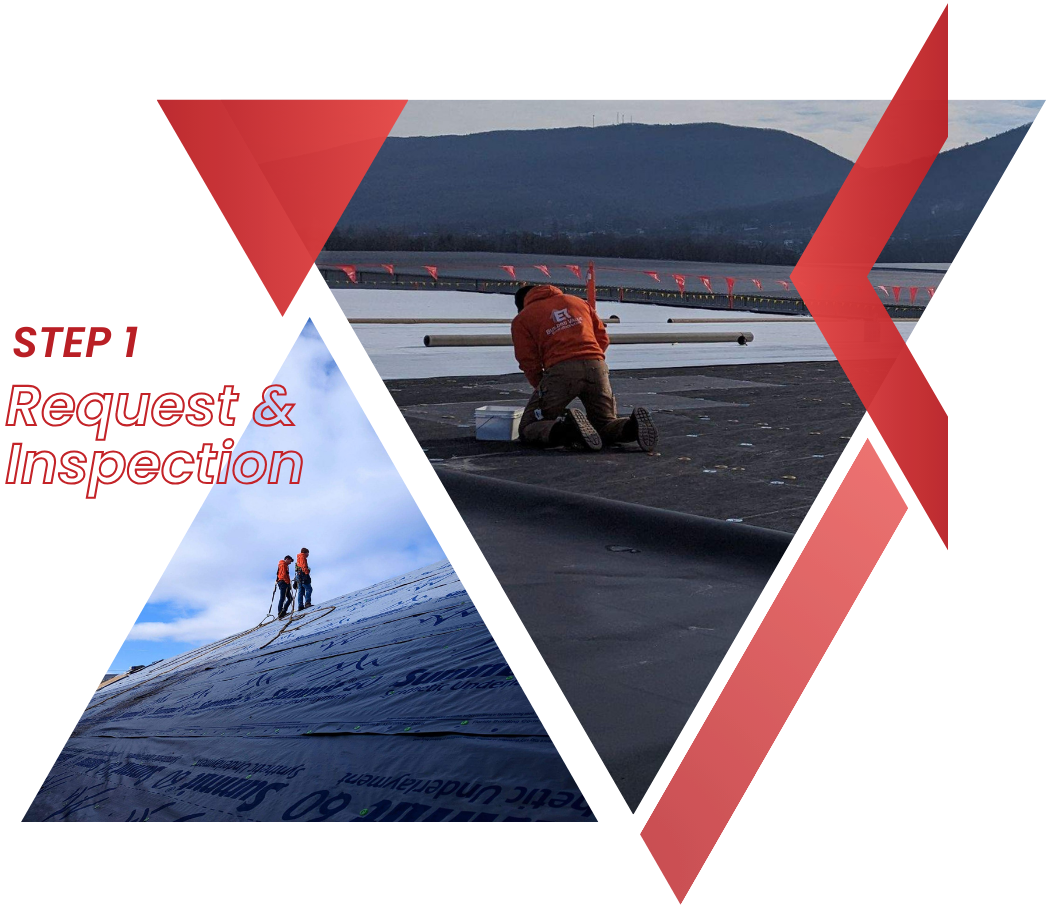
Step 1
Request and Inspection
From county facilities and schools to industrial parks and retail centers, we provide commercial roofing solutions tailored to Central PA’s weather, building codes, and infrastructure needs.
Includes:
-
Full roof walk-through and visual inspection
-
Grade assigned based on current condition
-
Photos and notes documenting damage, wear, or water entry
-
Evaluation of drainage, seams, insulation, and flashing
Step 2
Specifications and Recommendations
If the building doesn't come with an existing spec sheet, we work with the roofing materials manufacturer to develop one that meets performance and warranty goals. Based on your roof's grade and usage needs, we provide system recommendations and outline repair, restoration, or replacement options.
Includes:
-
Creation of custom specifications (if not provided)
-
System options: TPO, EPDM, PVC, metal, coating
-
Repair vs. replacement comparisons
-
Warranty types, energy efficiency, and expected lifespan
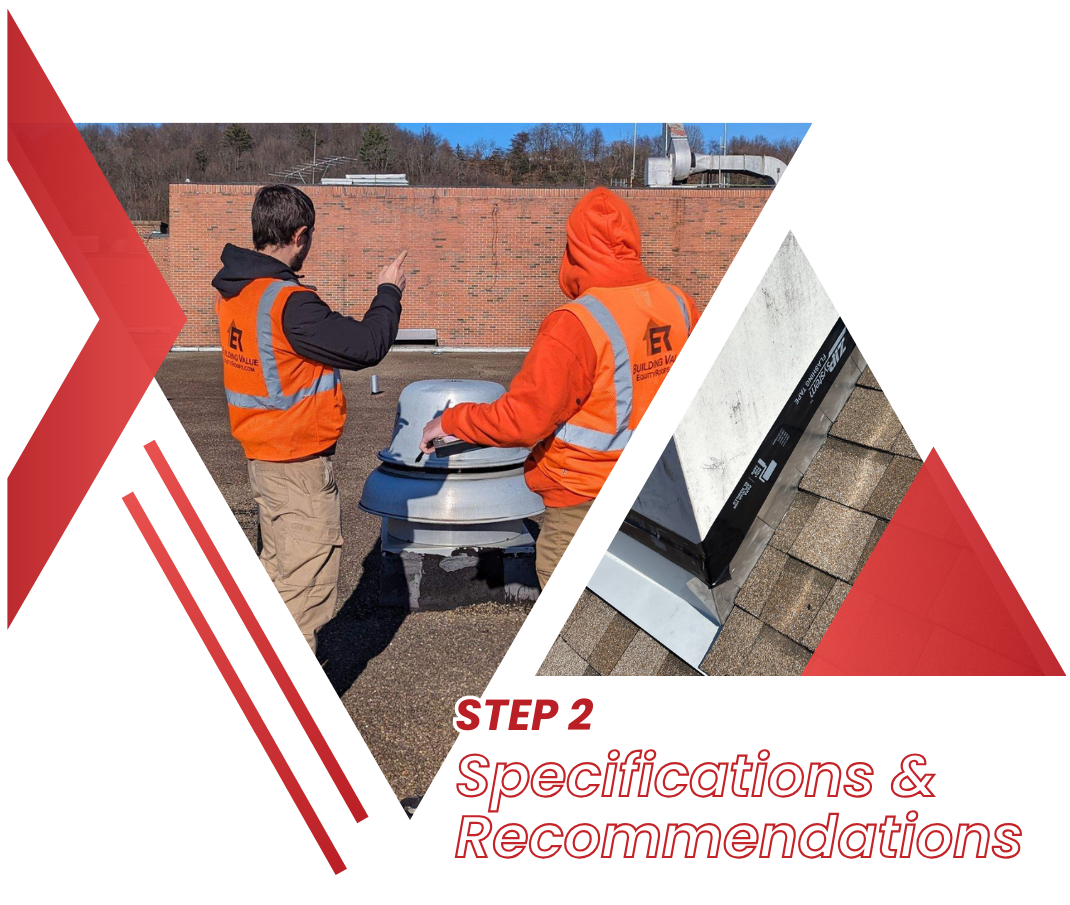
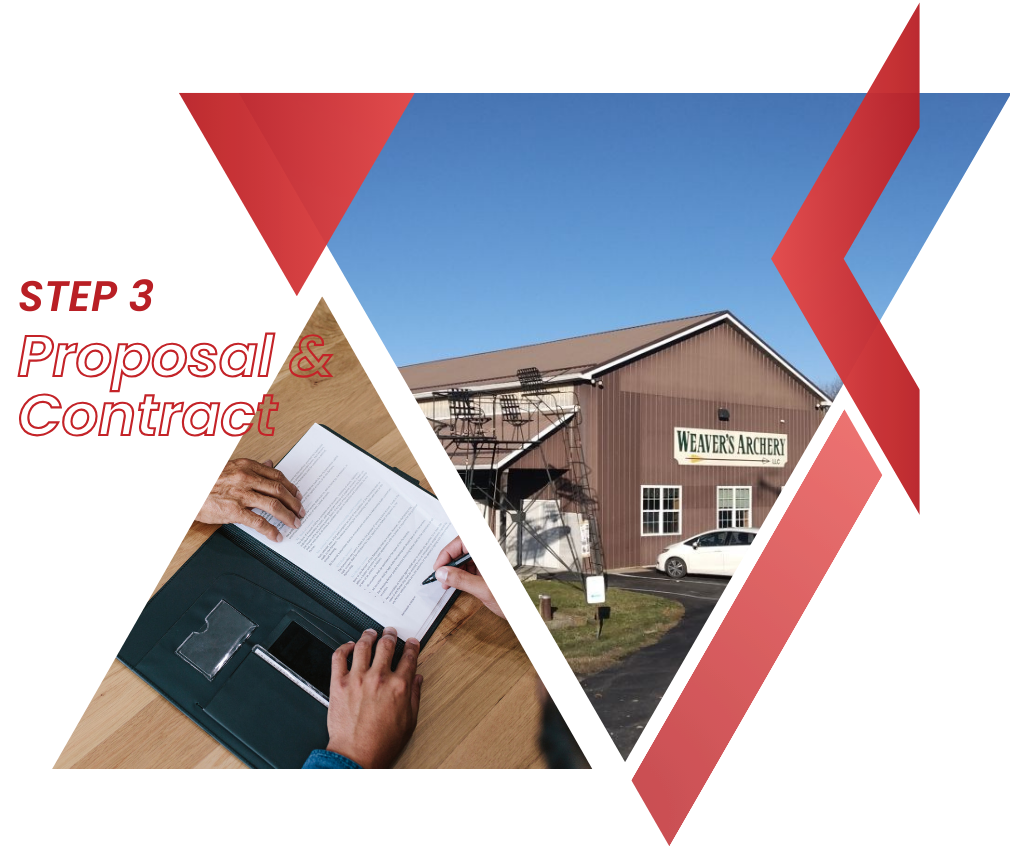
Step 3
Proposal and Contract
Once specifications are approved, we prepare a proposal with detailed pricing, scope, warranty coverage, and materials. A signature and 25% deposit are required to move forward.
Includes:
-
Written proposal with scope, specs, and pricing
-
Warranty details from material manufacturers
-
Contract agreement and deposit to initiate the job
Step 4
Scheduling and Mobilization
After contract execution, your project is scheduled. Your initial deposit is applied to the first invoice issued after mobilization. We coordinate staging, materials delivery, and access plans.
Includes:
-
Job added to the production schedule
-
Material orders and crew scheduling
-
Pre-construction coordination with building staff
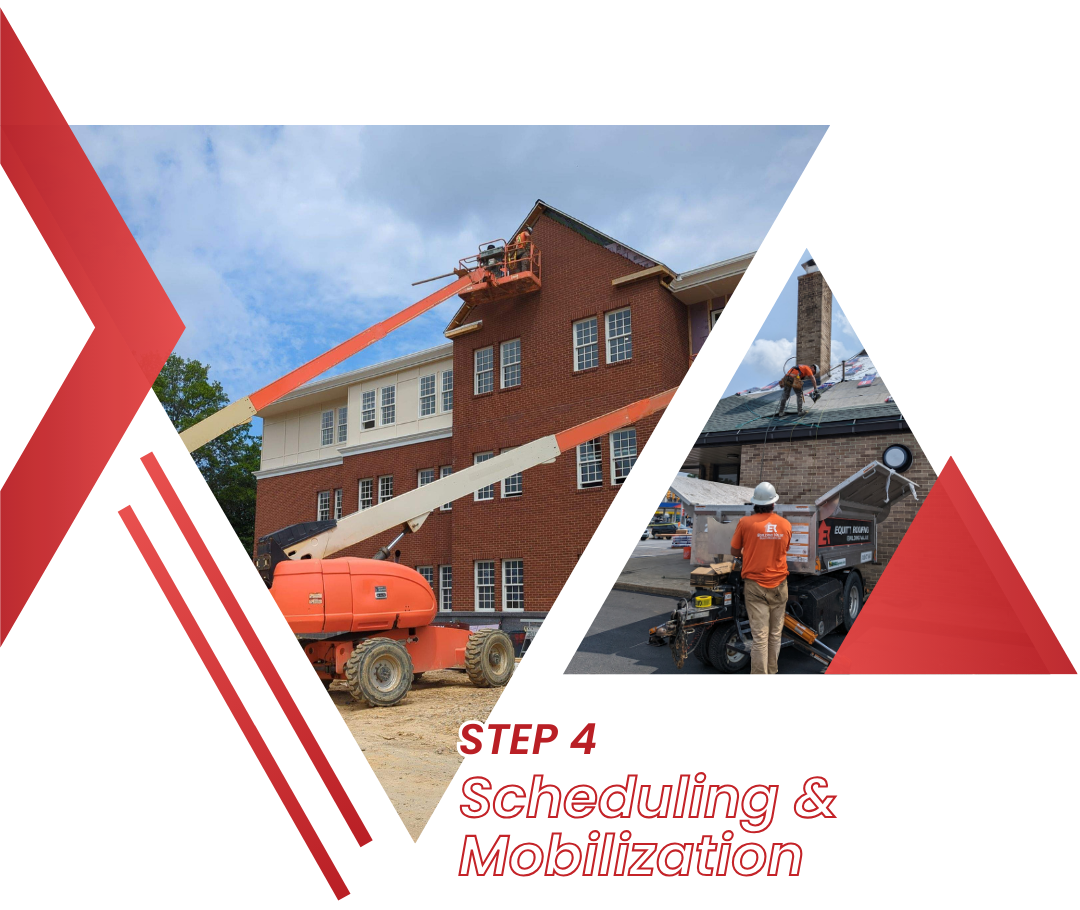
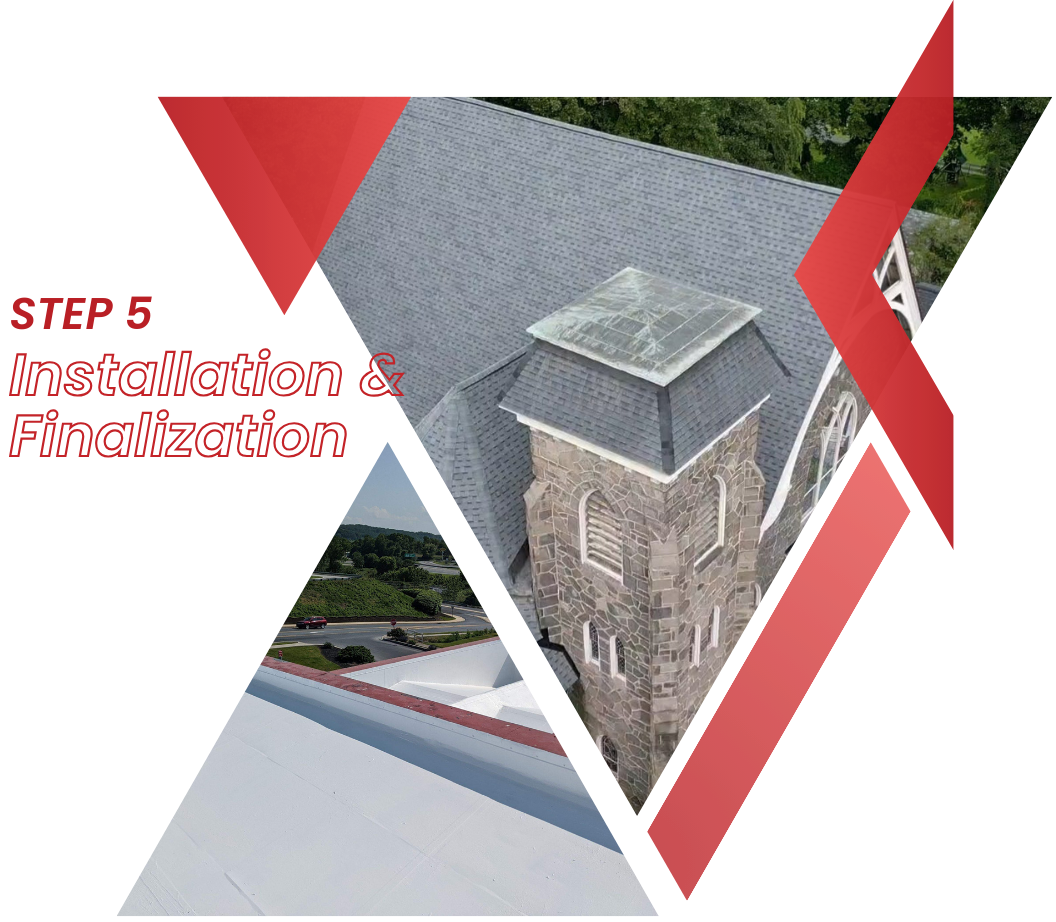
Step 5
Installation and Finalization
Our OSHA-trained crews install the system according to manufacturer and code requirements. Invoices are issued based on key milestones. Upon completion, we provide final documentation, warranties, and post-project support.
Includes:
-
Jobsite safety setup and protection of occupants
-
Removal of old materials (if required)
-
Installation of new roofing system
-
Final walkthrough, documentation, and cleanup
Why Our Process Works.
Clear documentation and system grading
Manufacturer-aligned specifications
Transparent milestones and billing
Warranty-backed materials
OSHA-compliant installation
Long-term support after project completion
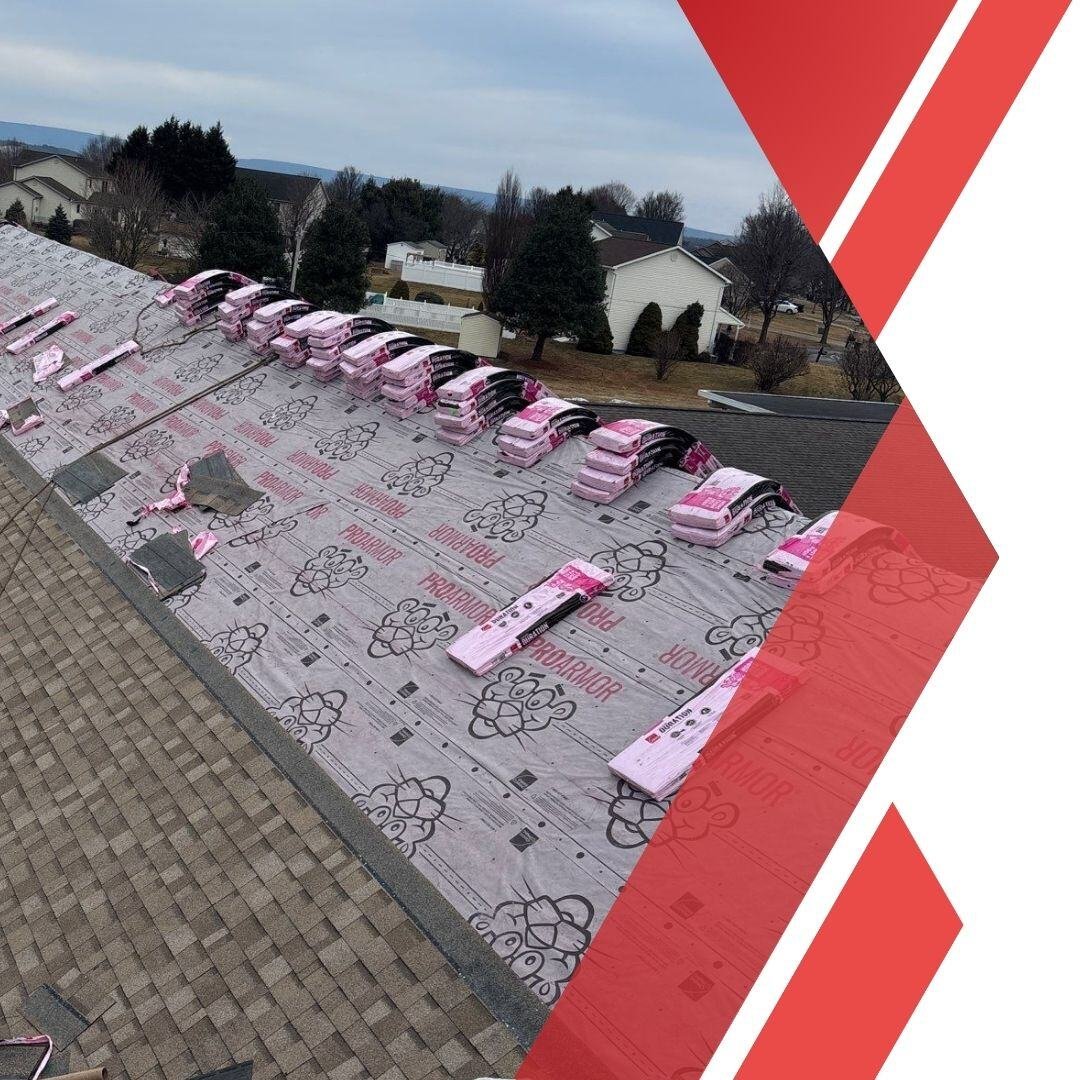
Frequently Asked Questions
-
How long does a roof evaluation take?
Most site visits take about 1–2 hours depending on roof size and accessibility. We’ll walk the full surface, document conditions, and answer any questions on the spot.
-
Do I have to commit to a full roof replacement?
Not at all. We recommend the most cost-effective solution based on your roof’s condition, which may include repair, coating, or partial restoration.
-
Will operations be disrupted during installation?
We coordinate carefully with your team to minimize noise, foot traffic, and disruption—especially in sensitive environments like schools or clinics.
-
How soon can you start after approval?
We’ll schedule your project based on urgency, weather, and material availability—typically within 1–3 weeks of contract signing.
-
What do I receive after the project is complete?
You’ll receive a warranty packet, photo documentation, and maintenance guidance. We’re also available for annual inspections and ongoing service if needed.